MSC Engineering is almost ready to test my water cooled Alta battery pack. Pack is ready to be swapped into my bike but need to finish all the plumbing first. System uses a small electric pump, remote radiator and a modified Alta pack. Currently, the pack has only two of the four modules actively cooled so I can get real comparison data under identical conditions.
The system will eventually feature a quick change dry break connector for attaching to an auxiliary chiller for cooling the modules below ambient for more thermal headroom. In addition, the chiller will allow cooling of the pack between motos while charging, a condition which currently takes an already hot pack and makes it even hotter.
The pack weight is unchanged, as there's no need for the 8 heavy heat spreaders. The only additional weight is the radiator, water lines, pump and of course, coolant. Probably 5-6 lbs. This rather extreme mod is only necessary if you have an issue with thermal limiting. Will it solve the problem? We'll find out over the next couple months of testing.
Details for the pack cold plate and retrofit is somewhat company private right now.
Note, I'm testing my A pack, which is more susceptible to thermal issues.
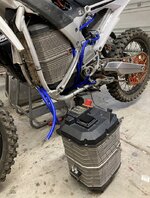
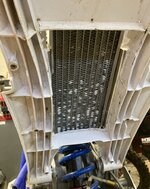
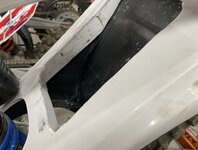
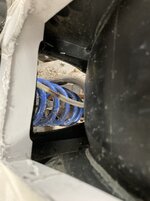
The system will eventually feature a quick change dry break connector for attaching to an auxiliary chiller for cooling the modules below ambient for more thermal headroom. In addition, the chiller will allow cooling of the pack between motos while charging, a condition which currently takes an already hot pack and makes it even hotter.
The pack weight is unchanged, as there's no need for the 8 heavy heat spreaders. The only additional weight is the radiator, water lines, pump and of course, coolant. Probably 5-6 lbs. This rather extreme mod is only necessary if you have an issue with thermal limiting. Will it solve the problem? We'll find out over the next couple months of testing.
Details for the pack cold plate and retrofit is somewhat company private right now.
Note, I'm testing my A pack, which is more susceptible to thermal issues.
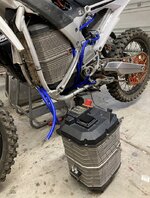
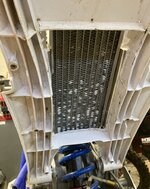
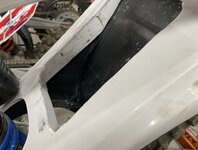
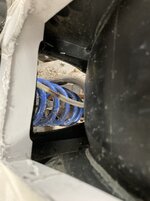