- Likes
- 2,799
- Location
- Pennsylvania
So by now most of us regular forum rats have heard of the dreaded "code 36" issue. Code 36 indicates a voltage imbalance which could happen for a whole host of reasons. When we are talking about the 2018 R packs the culprit will likely be a disconnected cell due to some issues they had in manufacturing with the wirebonding process. The "wirebond" refers to the small aluminum wire that connects both the positive and negative points on the cell to the module PCB. This wire will act as a fuse in the event of a cell failure that could potentially save the entire pack from further damage. Unfortunately we were told very little about this problem, and that is no fault of our ex Alta friends here as they likely were prohibited to talk about it. Fortunately most of our members here that had experienced the fault were able to get their packs replaced before the shutdown. Unfortunately @Bloak and myself were not so lucky. After much frustration trying to understand what was going on inside my pack and with very little info being disclosed, I decided to see for myself what exactly was the issue. Opening up the pack is not to be taken lightly and is VERY dangerous, you should be trained in electrical safety and have the appropriate equipment to do it. If you are at all unsure DON'T DO IT! We are talking about voltages that will kill you and a battery that could turn into a firebomb. Now that we got that out of the way let me show you what the actual problem looks like;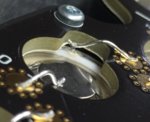
Take note to the upper most fuse on the negative connection of the cell. That is the bad connection, that's all it takes to cause this problem. I would take an wild guess that most if not all the wirebond problems were on that negative connection. Why did they all of a sudden have problems with R packs and not A packs? I think if we look at a comparison of the Panasonics used in the A packs to the Sonys used in the R packs we could make another assumption;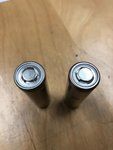
Sonys on left, Panasonics on right (picture courtesy of AltaWest). Note the somewhat wider, flatter lip where the negative connection is made on the Panasonics. We could conclude that this smaller target was just enough to cause a nightmare with the setup of their wirebonding machine.
What can be done to repair this? At this point there is no practical repair that we know of that would not somewhat negate the engineered safety that the OEM fuse wire provided. This is essentially one of the biggest problems with "rebuilding" packs, how to recreate the fuse wire that was engineered for the pack. I think in time there will be, but for now it's still a work in progress.
This is my take on the situation, and I may be wrong about some of the conclusions I have drawn. This post is meant to educate our members so they know what the heck we are referring to when we are taking about wirebonds and fuse wire, etc.
Feel free to discuss.
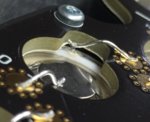
Take note to the upper most fuse on the negative connection of the cell. That is the bad connection, that's all it takes to cause this problem. I would take an wild guess that most if not all the wirebond problems were on that negative connection. Why did they all of a sudden have problems with R packs and not A packs? I think if we look at a comparison of the Panasonics used in the A packs to the Sonys used in the R packs we could make another assumption;
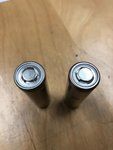
Sonys on left, Panasonics on right (picture courtesy of AltaWest). Note the somewhat wider, flatter lip where the negative connection is made on the Panasonics. We could conclude that this smaller target was just enough to cause a nightmare with the setup of their wirebonding machine.
What can be done to repair this? At this point there is no practical repair that we know of that would not somewhat negate the engineered safety that the OEM fuse wire provided. This is essentially one of the biggest problems with "rebuilding" packs, how to recreate the fuse wire that was engineered for the pack. I think in time there will be, but for now it's still a work in progress.
This is my take on the situation, and I may be wrong about some of the conclusions I have drawn. This post is meant to educate our members so they know what the heck we are referring to when we are taking about wirebonds and fuse wire, etc.
Feel free to discuss.